Steigerung von 70.000 MW pro Jahr durch ECOMAX®
Flexible und reaktionsschnelle Auto-Tuning-Lösung zur Maximierung von Leistung und Wirkungsgrad
- Ziele
-
- Ausgangsleistung erhöhen
- Wartungsausgaben senken
- Sektoren
-
- Industrie
- Anlage
-
- Schwere Gasturbinen
- Standort
- Plaquemine Parish, Louisiana, USA
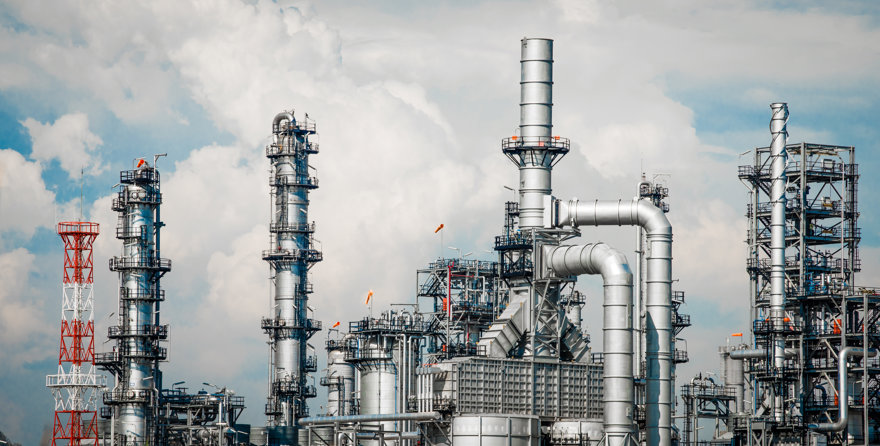
Projektübersicht
Eine chemische Raffinerie mit einer Flotte von vier 172-MW-7FA-Gasturbinen wollte im Rahmen ihrer langfristigen Nachhaltigkeitsziele die Leistung und den Wirkungsgrad ihrer Turbinen maximieren. Ohne eine Auto-Tuning-Lösung war man gezwungen, einen Drittanbieter mit der manuellen Abstimmung zu beauftragen, was sich negativ auf das Betriebsergebnis und die Leistung der Aggregate auswirkte. Außerdem wurde das MW-Leistungspotenzial nicht maximiert, was dazu führte, dass die Anlagen mehr Brennstoff als nötig verbrauchten, die Lebensdauer der Teile verkürzt und die CO2-Emissionen nicht minimiert wurden.
Mithilfe von ECOMAX® mit Tru-Curve konnten die Turbinen das ganze Jahr über bis zur Feuerungsgrenze laufen, was zu erheblichen Leistungssteigerungen (insgesamt mehr als 70.000 MW pro Jahr), einem geringeren Brennstoffverbrauch und erheblich reduzierten Emissionen (27.000 Tonnen CO2-Reduktion pro Jahr) führte.
Die Herausforderung
Das Werk war auf der Suche nach einer Lösung für den automatischen Abgleich sowie nach Aufklärung und Hilfestellung in Bezug auf die Abregelung seiner Turbinen und das richtige Lesen und Erkennen der Bedeutung von Warnungen des Verbrennungsdynamik-Überwachungssystems (CDMS).
Das CDMS gab ihnen die Möglichkeit, bei Überschreitung der Verbrennungsgrenzwerte Warnmeldungen zu erhalten. Sie hatten zudem eine Fernüberwachungsvereinbarung mit dem OEM, es war jedoch teuer und ineffizient, jedes Mal, wenn das CDMS ein Problem anzeigte, jemanden zu holen, der die Aggregate manuell abstimmte. Das gegenwärtig vorhandene Tool diente lediglich der Berichterstattung und Identifizierung und bot kaum Möglichkeiten zur internen Lösung von Abstimmungsproblemen.
Um die Effizienz zu maximieren, benötigte das Unternehmen eine flexible und reaktionsschnelle Lösung, die innerhalb des Werks gesteuert werden konnte. Erschwerend kam hinzu, dass die Anlagen ursprünglich nicht über Roh-NOx-Sonden verfügten, was ihre Flexibilität innerhalb des Regelungssystems einschränkte.
(Foto: Verbrennungshardware vor dem Einbau von ECOMAX®)
Die EthosEnergy-Lösung
Nach Gesprächen mit dem Engineering-Team von EthosEnergy beauftragte das Werk EthosEnergy mit dem Einbau von ECOMAX® mit Tru-Curve-Auto-Tuning in einem der Aggregate. Dies ermöglichte eine größere Flexibilität und eine Steuerung aus der Leitwarte über ein computergestütztes Turbinensteuerungsprogramm. Dadurch war es nicht mehr erforderlich, dass ein Tuner nach einer Brennkammerinspektion, einer Heißteilinspektion oder einer Hauptinspektion zum Standort kommen musste, was Planungs- und Kosteneinsparungen mit sich brachte. Es ermöglichte auch die Anpassung der maximalen Feuerungstemperatur im Winter und im Sommer bei gleichzeitiger Abschwächung der Brennkammerdynamik, eine längere Lebensdauer der Bauteile und die automatische Abregelung der Gasturbine, wenn die Verbrennungsdynamik nicht unter den festgelegten Grenzwerten gehalten werden konnte.
Da das Aggregat immer abgestimmt war, konnte es das ganze Jahr über bis zur Feuerungsgrenze betrieben werden, wodurch die Leistung des Aggregats wirklich maximiert wurde.
Nach einem vollständigen Zyklus zuverlässiger Betriebszeit und einer Überprüfung der Verbrennungshardware wurde dasselbe System erfolgreich in den verbleibenden drei Gasturbinen am Standort und später in acht weiteren Anlagen für die Muttergesellschaft in Nordamerika installiert, darunter die folgenden Maschinentypen: 7FA, 7EA und 501D.
(Foto: Verbrennungshardware nach dem Einbau von ECOMAX®)
Key Results
- Firing temperature increase from 2400 Fahrenheit to 2424 Fahrenheit
- Observed one MWe per 10 degrees of firing temperature increase for a total output increase of 9.6 MWe
- Observed 8 mlb/hr (8000 pph) of HP steam flow per each 10 degrees of firing temperature increase for a total output increase of 10.4 MWeqv. of steam
- 20 additional MWs for 98 MMBtu of additional fuel (4.9 INHR)
- 465k MMBtu per year of fuel savings
- 27,200 tons per year of CO2 reduction from increased steam efficiency and lower CO from tuning improvements
- Over 70,000 new MWs per year produced at 4.9 MMbtu per MW
Über ECOMAX® mit Tru-Curve
Die Verbrennung mit einer mageren Premix-Flamme kann die NOx-Emissionen niedrig halten; eine zu magere Flamme kann jedoch zu Instabilität führen. Diese Instabilität (Verbrennungsdynamik) kann zu teueren Schäden an der Brennkammer und den nachgeschalteten Komponenten führen. Die manuelle Abstimmung erfordert ein konservatives Gleichgewicht zwischen der Einhaltung der Emissionsvorschriften und der Verbrennungsdynamik.
ECOMAX® ist eine vollautomatische Plattform, die die Emissionen steuert, einen flexiblen Betrieb ermöglicht und den thermischen Wirkungsgrad eines Gasturbinenkraftwerks erhöht. Das Basissystem automatisiert die Abstimmung für die kontinuierliche Einhaltung von NOx- und CO-Werten, die Flammenstabilität und eine akzeptable Verbrennungsdynamik.
Das Brennstoff-Luft-Verhältnis der Turbine ist ein Schlüsselparameter, der die Leistung der Gasturbine (und des Kraftwerks) beeinflusst. Eine Erhöhung des Brennstoff/-Luftverhältnisses der Turbine im Grundlastbetrieb verbessert zwar die Ausgangsleistung und den Wärmeverbrauch, wirkt sich aber nachteilig auf die Emissionen und die Brennkammerdynamik aus.
Tru-Curve® ist ein Modul für ECOMAX®, das das Brennstoff/-Luftverhältnis der Turbine im Grundlastbereich erhöht. Konkret handelt es sich um eine Verschiebung des Verbrennungsbetriebs an einen Rand des Betriebsbereichs, während ECOMAX® weiterhin die Emissionen und die Brennkammerdynamik innerhalb des Bereichs steuert.
Wichtigste Ergebnisse
- Erhöhung der Feuerungstemperatur von 2400 °F auf 2424 °F
- Beobachtete Erhöhung um ein MWe pro 10 Grad Feuerungstemperatur bei einer Gesamtleistungssteigerung von 9,6 MWe
- Beobachteter Hochdruckdampfdurchsatz 8 mlb/h (8000 pph) pro 10 Grad Feuerungstemperaturerhöhung für eine Gesamtleistungssteigerung von 10,4 MWeqv. Dampf
- 20 zusätzliche MW für 98 MMBtu zusätzlichen Brennstoff (4,9 INHR)
- 465T MMBtu pro Jahr Brennstoffeinsparungen
- 27.200 Tonnen CO2-Reduktion pro Jahr durch erhöhten Dampfwirkungsgrad und niedrigerer CO-Gehalt durch Tuning-Verbesserungen
- Über 70.000 neue MW pro Jahr mit 4,9 MMbtu pro MW produziert