Autotune to perfection with ECOMAX®
Our precision autotuning and combustion optimization platform uses live data so that you can operate on your own terms, even in extreme conditions. Our advanced technology and patented sensor-based algorithm continually monitors and automatically fine-tunes combustion parameters, responding to live metrics to maintain NOx and CO emissions compliance, flame stability and combustion dynamics, while ensuring optimal power output.
ECOMAX® sets the standard for autotuners, optimized to your specification and outperforming in extreme conditions where others cannot operate.
The platform has been installed on 125+ gas turbines at over 50+ sites globally, including 99 installations on Frame 7F gas turbines.
Sales
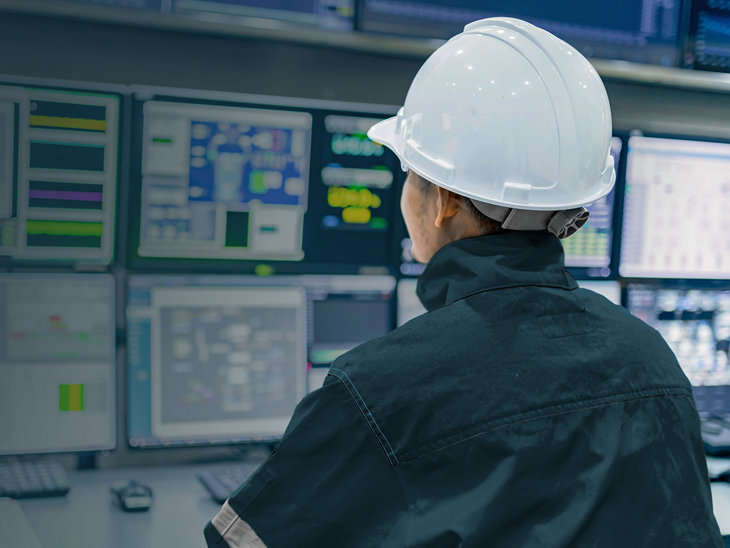
The ECOMAX® advantage
Reliable precision-performance units, even in extreme conditions
ECOMAX® utilizes a patented sensor-based algorithm to analyze live gas turbine combustion data, enabling continuous adjustment of parameters for optimal performance. Unlike model-based systems with predetermined parameters that prescribe power and emissions output, ECOMAX® reacts solely to real-world conditions, automatically making tuning decisions based on these measurements. This approach ensures precision performance operations, even in extreme and infrequent conditions, making it the perfect choice for reliable and efficient plant operations. This is what we call the ECOMAX® advantage.
With our advanced platform providing improved operational visibility, you can confidently operate your plant at full power more frequently, reducing instances of blowout or shutdown. This maximizes availability and reliability. Additionally, when plants are brought back online after shutdown—whether due to accident, fault, or intent—ECOMAX® seamlessly resumes operations from where it left off. Instead of restarting the system, it intelligently detects conditions but refrains from making changes until the plant is fully operational again.
Turbine optimization that maximizes ROI and minimizes costs
ECOMAX® significantly reduces maintenance spend and lowers maintenance costs by eliminating manual tuning requirements and the need for seasonal control engineers. With our advanced autotuning capabilities, operational adjustments are made in minutes, minimizing downtime and maximizing profitability.
It safely and efficiently extends operational turndown, providing you with more opportunities to operate and generate revenue. Our platform eliminates the need for control upgrades that are not mandated, offering a streamlined and cost-efficient approach to optimization.
Additionally, our solution delivers increased baseload megawatts through optimization via Tru-Curve, maximizing power output and efficiency, thus unlocking additional revenue potential for your operation. Our responsive platform enhances operational efficiency, reduce costs, and maximizes your revenue potential.
Automated and fully customizable for unparalleled operational flexibility
The ECOMAX® combustion tuning platform provides an automated, fully customizable solution to achieve customer-determined operational objectives.It is unparalleled in its versatility. Not only is it hardware agnostic, seamlessly integrating with any hardware manufacturer, but it's also fully customizable. Our solutions enable you to add optimization software modules to match your specific operational needs and goals. Whether you're focused on improving heat rate, reducing downtime, or maximizing efficiency, ECOMAX® provides unique operational flexibility and scalability.
Our autotuning capabilities enable your operation to consistently perform at its peak, automatically adapting to changing conditions without the need for manual intervention. Take control of your plant with ease and flexibility, eliminating the need for seasonal manual engineer tuning, third-party interventions, or restrictive operating parameters. With subscription and fixed payment options available, you can operate precisely how you need to, ensuring maximum performance.
Achieve low-emission compliance with optimized power performance
In today's regulatory landscape, where emissions regulations on power generation are tightening at state, local, and national levels, the demand for low-emissions power generation has never been higher.
Our exclusive automated tuning technology continually monitors gas turbine combustor performance. It precisely adjusts key combustion control parameters using live data to uphold NOx and CO compliance, ensure flame stability, improve plant heat rate, and maintain acceptable combustion dynamics. ECOMAX® achieves this delicate balance by finding the optimal fuel-burn to power ratio, seamlessly merging emission reductions with enhanced power output. Whether in combined or simple cycle operations, ECOMAX® empowers you to reduce pollutant emissions without compromising gas turbine acoustic stability or overall plant performance.
Case Study - 70,000 MW per year increase via ECOMAX®
A petrochemical plant with a fleet of four 172MW 7FA gas turbines was looking to maximize the performance and efficiency of their units as part of their long-term sustainability goals. Without an auto-tuning solution, they were forced to contract a third-party to perform manual tuning which negatively impacted bottom line and unit performance. It also didn’t maximize MW output potential, which caused the units to burn more fuel than needed, decreased part life, and failed to minimize emissions.
ECOMAX® with Tru-Curve allowed the units to run up to the firing limit year-round, generating substantial gains in performance (a cumulative 70,000+ MWs per year), reduced fuel consumption, and greatly reduced emissions (27,000 ton per year CO2 reduction).
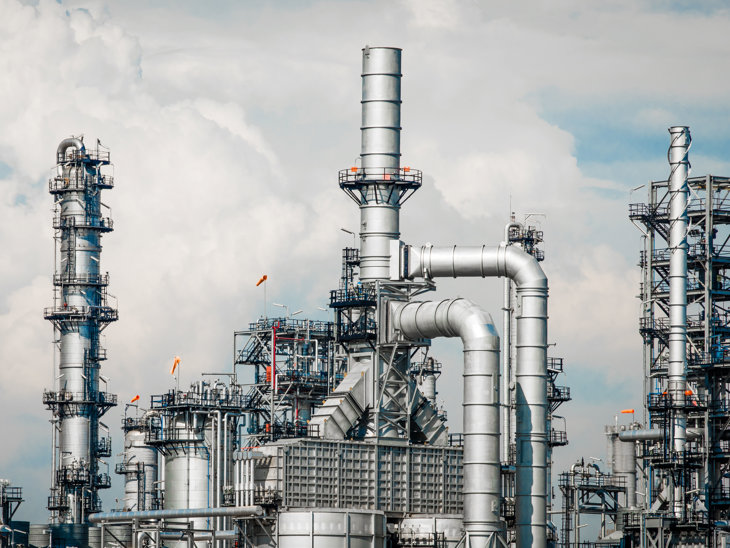
ECOMAX® optimization modules
Choose from optimization software modules that suit your unique operational needs and goals
Unlock your plants full potential with our diverse suite of optimization modules designed to address and fine-tune specific operational challenges and objectives. Whether you aim to maximize efficiency, reduce downtime, or enhance reliability, our customizable solutions allow you to prioritize and optimize plant performance according to your unique requirements. From initial setup to ongoing enhancement, Ecomax® Optimization modules provide the flexibility and scalability required to achieve operational reliability, peak performance and operational excellence.
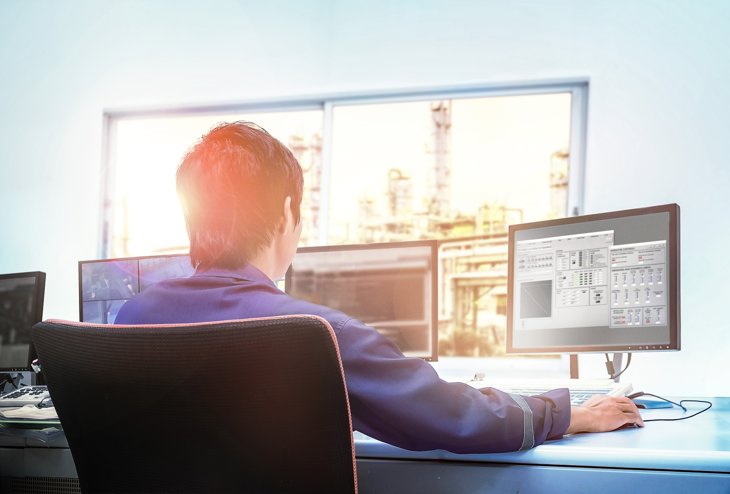
ECOMAX® CDMS
Advanced monitoring instrumentation for safeguarding turbine components and optimizing performance
Our advanced Combustion Dynamics Monitoring Systems technology continuously monitors the acoustic behavior of each combustor, proactively identifying and mitigating high dynamic amplitudes to safeguard against potential component damage. With permanent monitoring capabilities and two distinct system types, Ecomax® CDMS ensures continuous surveillance and early detection of hardware failures, empowering operators to take preemptive action and maximize operational efficiency. While CDMS is typically essential for operating ECOMAX® automated tuning technology, there may be exceptional circumstances where its usage is not required.
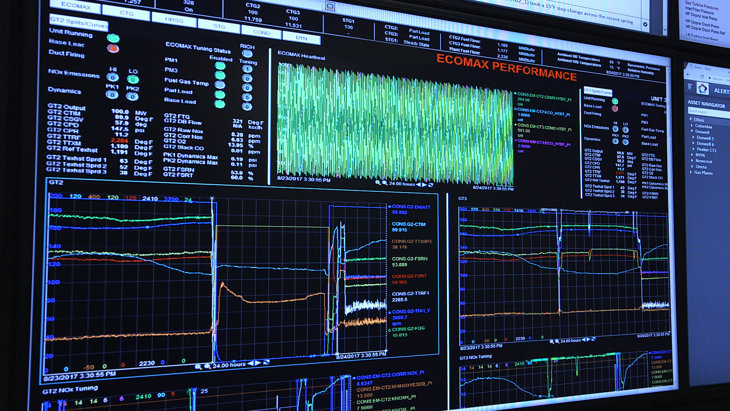