Gas turbines down at 3 different plants
Putting out the fires during a busy outage season
- Goals
-
- Reduce Forced Outage Rate
- Sectors
-
- Power generation
- Asset
-
- Heavy Gas Turbine Maintenance and Services
- Location
- Northern and eastern, US
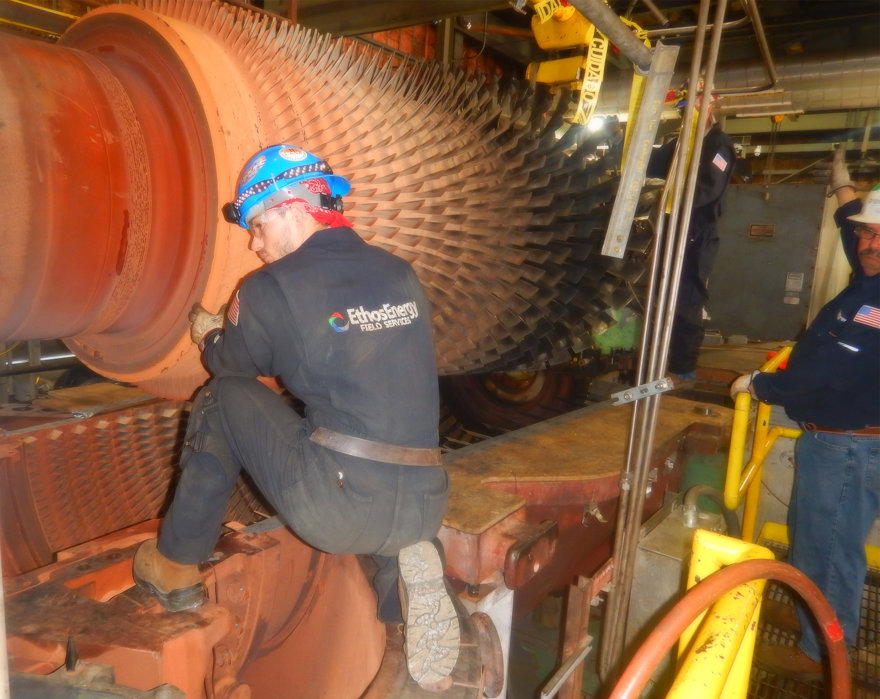
Challenges, challenges, challenges
Bad things come in threes
Imagine this. A key unit in your facility goes down. You’re immediately facing a struggle to get it back online as quickly as possible. Every day that it remains out of action, the hit to your bottom line grows and grows.
Now imagine it’s the height of outage season. Suddenly the difficulties you face have intensified. With labor and materials in short supply, will you be able to find a provider with the experience and knowledge base to get your unit back up and running?
That was the situation facing our client, a major utility in the US, over the winter of 2021/22 and into the spring. Not once, not twice, but three times.
Three different power plants. Three emergency situations. Three headaches to deal with.
All within a short space of time.
Extensive damage at power plant 1
Compressor failure calls for comprehensive know-how
Going into 2022, our client knew it was going to be critical to have their units operational for the summer run. Miss your dispatch and – when the resulting penalties kick in – you can lose everything you would have made for the year.
So when they suffered a compressor failure at their peaking power plant in Indiana, they knew they had a job on their hands. Foreign object damage (FOD) had taken out the whole compressor. This wasn’t something the client’s internal crew could deal with. So our client called on our expertise and experience.
In December 2021, we worked on planning an outage, mobilizing all the replacement components the unit needed, including new compressor blades and vanes. No sooner had the new year begun than we were on site disassembling the machine.
But it turned out the damage was far more extensive than previously thought. When looking downstream, we discovered further issues. So we migrated our repairs into a major outage and cleaned everything up.
Two days to mobilize at power plant 2
Three cheers for union field services
Not long after we had gotten to grips with the issues in Indiana, our client experienced a forced outage at a combined-cycle power plant in Florida. This was due to second-stage blade failure on a GE 7FA gas turbine. Extremely high vibrations led to the machine tripping and causing extensive damage in the hot section down through the exhaust.
This second power plant was scheduled to carry out a major outage in the fall of 2022. But our client asked us if we could bring it forward. The challenge was they wanted us to mobilize and be on site within just two days.
While this was a great opportunity, the spring of 2022 was the busiest outage season we had seen in years. But our union field services team doesn’t know the meaning of “no can do.” Fast and responsive, they stepped up to the plate and made sure we answered the challenge of the tight timetable. We were on site within two days and fully staffed with experienced crews within four days.
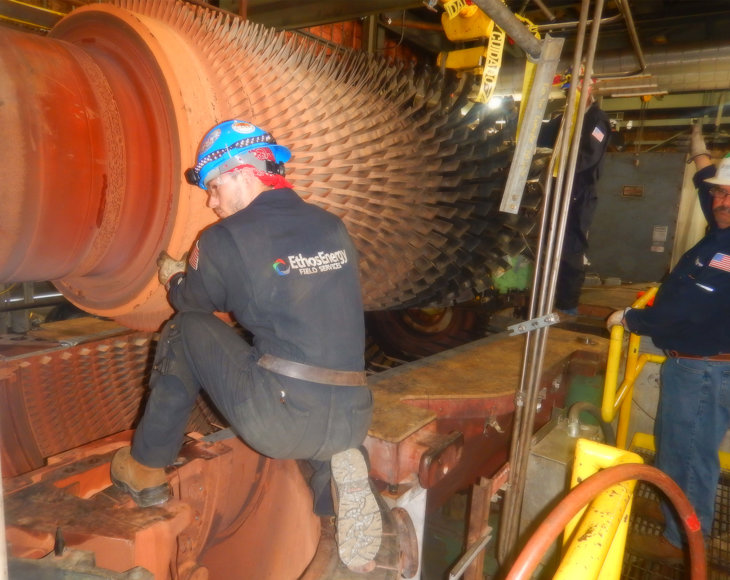
Overlapping issue at power plant 3
Burning up another issue at another facility
But while we were working at the second power plant, there was a problem at another of our client’s facilities in Florida. This peaking power plant started experiencing combustion issues on one of its 7EA units. Our client asked us to carry out a modified combustion inspection.
As it happened, this was during a lull in the major outage at the second power plant. That meant we were able to support the third power plant with the same field service personnel. We sent them 90 miles up the road where they performed a fuel nozzle change-out. A few more issues came to light but within five days we had the machine up and running.
But the completion of the major outage didn’t spell the end of our client’s problems.
Back On Site at Power Plant 2
Fighting fires once more
A week after we had demobilized from the combined-cycle power plant in Florida, there was an explosion and a fire. Fortunately, nobody was injured, and we would come to discover that it was not a result of our previous work. But our client was understandably concerned.
Once again, we were able to mobilize within two days. On inspection, we ascertained that there was a crack in the atomizing air vessel containing the filter strainer.
We launched a 30-day outage. Stripped everything down. Repaired and refurbished the machine, replacing combustion components and various other items. And got the unit back up and running.
You’re in safe hands with EthosEnergy
At EthosEnergy, safety is of the utmost importance – as it is for this particular client. So it was a great achievement not only to have answered the call at these three sites, but to have done so without any safety issues.
So pleased was our client that their Senior Vice President of Plant Operations made a point of praising our teams for their efforts during a meeting with their leadership.
The agility and flexibility demonstrated by our union field services teams ensured our client’s facilities were all fully operational for the key summer season. A season that saw particularly high demand in 2022. And one in which our client’s units were able to run each and every day.
Key Results
- Responsive union field services team demonstrates flexibility
- Rapid mobilization at three different sites during peak outage season
- Work undertaken with no safety issues
Looking for more?
We have a wide portfolio of case studies with proven results in the power generation industry. View our hand picked examples to read how our maintenance services can help reduce forced outage rate.