The Gateway to Maximize Reliability and Performance is ECOMAX® Auto-Tuning
- Date
- April 16, 2025
- Category
- Impact
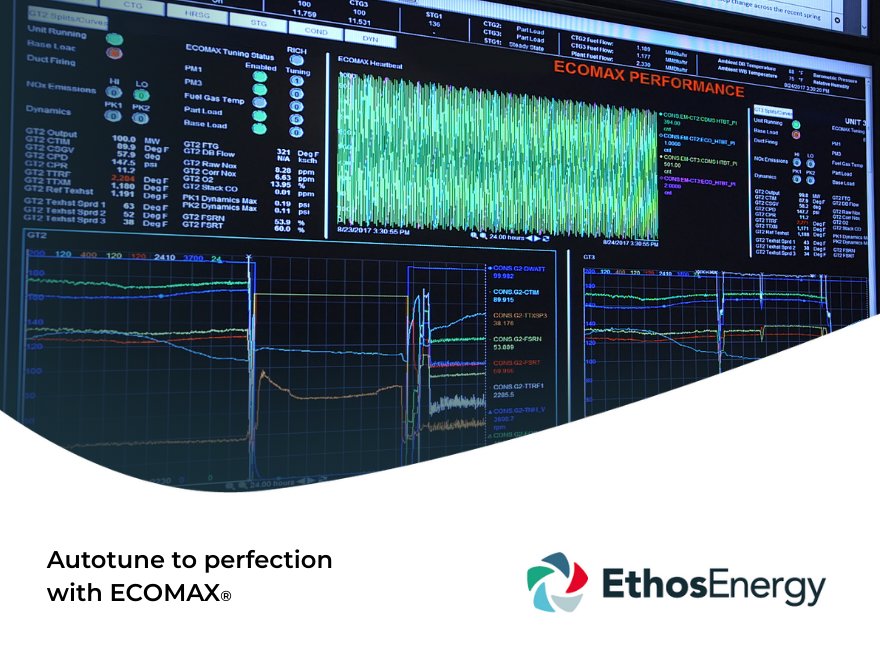
How auto-tuning enhances efficiency and emissions control
Gas turbine operators today are under constant pressure to keep emissions within permitted levels while reliability and outputs must remain high.
In reality, when you’re relying on traditional manual tuning methods or limited model-based systems, it’s impossible to avoid excursions under extreme events and simultaneously operate at top performance.
That’s where ECOMAX comes in.
Combining auto-tuning and combustion optimization enables users to stay compliant, maximize turbine performance, and continue operating under extreme environmental changes.
Here, we’ll explore how ECOMAX works, and why more and more operators are making the switch.
How ECOMAX works: real-time tuning that reacts to reality
Manually tuning gas turbines with dry low emissions (DLE) systems has been the norm for decades. Many plants still bring in manual tuners twice yearly to tweak parameters for the season ahead.
It’s not cheap, and it’s not always effective.
These tune-ups can be overly cautious to avoid tripping permit limits. They factor in conservatism to maintain emissions as the weather warms through summer or cools through winter.
This conservative approach comes at a cost – power output (affecting your performance) and efficiency (affecting your cost-effectiveness). Many times, the unit’s total output is limited (derated) just to maintain emissions. This derating for emissions (is really a decrease in firing temperature) and can be the most significant and hidden loss in performance.
ECOMAX changes everything.
A sensor-driven, patented auto-tuning platform, ECOMAX continuously adjusts combustion parameters in real time – without human intervention.
Installed as a standalone controller, ECOMAX integrates directly with turbine control systems, using advanced algorithms to monitor combustion dynamics (flame stability), NOx, and CO. This allows it to instantly adapt its operating parameters to ambient conditions, fuel variability, and any other influence – in real time.
No guesswork. No waiting for someone to notice a problem.
Because ECOMAX measures and responds to actual turbine conditions, rather than relying on predictions in an ideal model, it can tune more accurately – and without the large conservatism of manual methods.
Operators can run up to the optimal firing temperature without risking emissions compliance violations or hardware stress from combustion dynamics. This means maximized power and heat rate and continued operational stability – even during extreme scenarios.
Presenting new possibilities with plug-and-play integration
Despite its advanced capabilities, ECOMAX is straightforward to deploy, with installation usually taking less than a week, integrating rather than retrofitting your current turbine control system.
Once installed, it operates independently and can be tailored to each site’s specific configuration, control system, and emissions requirements. Operators maintain one interface to run the unit and have the ability to manipulate ECOMAX as economic conditions change.
Working alongside your existing control system, ECOMAX adjusts parameters like inlet guide vane angles, inlet bleed heat, and combustion curves – just like a manual tuner would, but smarter, faster, and all the time.
ECOMAX is compatible with:
● GE Heavy Frame Units (including all DLN versions and water or steam injection on Frames 6B, 6F, 7B, 7E, 7F, 9E, and 9F)
● Siemens/Westinghouse Frames 501D and 501F
● Most major control systems (including GE SpeedTronic Mark V, V1, and V1e, Emerson Ovation, and EthosEnergy icon)
● OEM and non-OEM combustion hardware
● Any fuel composition, including dual-fuel setups
With more than 125 installations across 50+ sites globally, ECOMAX has proven it can scale all over the world – from single-unit, simple-cycle plants to large, combined-cycle fleets.
The fast and flexible: the real ROI of auto-tuning
Most plants recoup their investment in ECOMAX within two years. Simply replacing regular manual tuning events is often enough to result in a full return on investment.
The real value, however, comes in the performance improvements once you’re no longer limited by conservative, static combustion tuning.
After installation, ECOMAX helps you:
● Add up to 1-1.5% more power output
● Improve heat rate performance by 0.25-0.5%
● Reduce wear and tear on combustion hardware
● Limit the frequency of forced outages
● Avoid regulatory fines
It also gives operators far more flexibility in how they run. For cycling plants or peaking units, ECOMAX enables deeper turndown – instead of shutting down completely, you can drop to a lower minimum load.
This alone can shift your maintenance approach from starts-based to hours-based – saving further operational costs over time.
Proven performance, even in the harshest conditions
Resilience in the Texas freeze
In February 2021, a historic winter storm hit Texas. While demand soared, many of the state’s power generation assets struggled to stay online in the extreme cold, creating a grid crisis.
One combined-cycle plant had a unique setup: two power blocks, one tuned with ECOMAX, the other with a competitor’s auto-tuner.
The result? The ECOMAX-tuned block stayed fully operational throughout the storm, avoiding catastrophic downtime. The other block failed under the stress, staying offline for days.
That uptime didn’t just protect the grid – it saved the operator $4 million per hour in potential losses. Within weeks, the operator replaced the competitor’s system with ECOMAX-equipped turbines across their six other sites.
An annual gain of 70,000 MWh
Operators at a large petrochemical facility wanted to improve the sustainability of their fleet of 7FA turbines. Manual tuning was inefficient, and all units were underperforming. By not reaching their full output potential, high emissions and fuel consumption were eating into their margins.
The fix? ECOMAX. After installation with the Tru-Curve module, the plant could run closer to the firing limit year-round, without violating emissions limits, resulting in:
● 70,000+ MWh/year added to the site’s output
● CO2 reduced by 27,200 tons/year
● 465,000 MMBtu/year saved in fuel
In addition, as ECOMAX can be operated directly from the control room, the site no longer needs to invest in costly third-party tuners after inspections or outages.
In Turkey, a newly acquired gas-fired 775MW power plant had a problem: its 9FA turbines with non-OEM modifications were causing repeated combustion trips. The OEM offered to replace key components, quoting unit replacements at $20 million apiece.
Instead, the operator turned to EthosEnergy to trial ECOMAX.
For its first deployment of non-OEM-upgraded F-class turbines, ECOMAX was a major success. It stabilized combustion, eliminated unexpected shutdowns, and restored reliability even during large temperature swings.
This not only saved the operator $15 million in capital expenditures, but it also extended the value of their existing equipment.
Built for today, ready for tomorrow
ECOMAX doesn’t just help operators run better – it helps prepare for the unknown.
Whether that’s weather extremes, economic changes, or fluctuating fuel quality, ECOMAX adapts in real time. Its auto-tuning gives operators the perfect balance between reliability, flexibility, efficiency, and sustainability.
From added megawatts and fuel savings to improved reliability and fewer emissions headaches, ECOMAX delivers measurable value – fast.
Are your units still relying on manual tuning or running conservative settings to avoid permit violations? There’s a smarter way.