Uncovering hidden issues with a Thermal Performance Audit
Recommending action points and quantifying their impact
- Goals
-
- Decrease Heat Rate
- Increase Power Output
- Increase Steam Production
- Sectors
-
- Power generation
- Asset
-
- Heavy Gas Turbine Maintenance and Services
- Steam Turbines
- Location
- Midwest, US
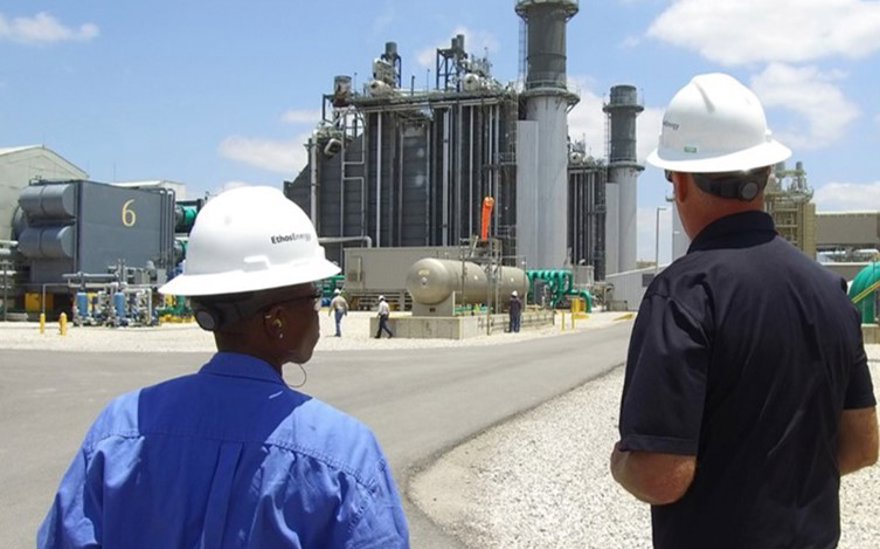
The Challenge
Pinpointing a power loss problem
The power generation market is becoming more competitive. It has never been more important to make sure you are getting the best performance from your plant. But how can you be sure you are getting the most out of all of your plant assets?
If you are an experienced operator, you might be able to detect a fractional decrease in plant output. But it is very difficult to identify that over changing ambient conditions. And pinpointing the root cause is even more difficult; there can be hidden issues at play.
That was exactly the position for our client, a 4x2 combined-cycle power plant in the Midwestern United States.
We were providing remote monitoring through our Plant Health & Diagnostics system (PHD Advance). That enabled us to alert our engineers and the plant to with the plant’s performance. The power output was down by around 2.5 MW and it was degrading at a faster rate than expected.
The question that remained, though, was why. What was causing such a steep decline in performance?
The Solution
Identifying the issues, actions, and impact
Uncovering the cause of the performance issue was not the only concern. Because when your plant suffers a power loss, not only do you want to identify the cause, you want to know what you can do to address it. And whether a proposed solution actually makes financial sense…
That’s why our client engaged us to carry out a Thermal Performance Audit.
Rather than just focusing on the gas turbine performance, we conduct a deep analysis of the entire plant. Our experienced engineers benchmark each system against OEM performance data and industry expectations. This holistic approach allows us to consider the knock-on effects of potential remedial actions.
Here, one of the issues we were able to identify was a problem with the inlet fogging system’s cooling temperature.
The fogging system was essentially independent of any monitoring of the rest of the plant. It was not tied into the plant historian and operating data was not easily accessible. So the plant’s operators had no indication there was a problem there. They had no way of seeing how the fogging system’s performance compared to what was expected.
But we make a point of pulling in weather data from the surrounding area, such as from the local regional airport. This indicated the fogging system was not cooling the inlet air as much as it should, and it was performing inconsistently across different weather conditions. This was costing the plant 3.5 MW and 72 Btu/kWh for each of the two affected units.
We also identified a number of other issues. For each one, not only did we recommend an action step but we also quantified its likely impact – in terms of both the projected power gains and the expected cost savings.
The Impact
A quantified path to saving millions and recovering MWs
We were able to recommend a series of actions that could save the plant over $3 million a year. Those included:
Decreasing the inlet fogging system’s cooling temperature by 2°F
- This would recover 3.5 MW and 72 Btu/kWh for each of the two affected units. By taking our recommendation, the plant earned an estimated $600,000 over the course of the year.
Lifting self-imposed duct-firing temperature constraints
- Up to 20 MW per unit could be recovered. Even a 10% recovery on each unit could result in additional earnings of over $1.6 million a year.
Reducing the temperature of the by 3–4°F
- The current temperature was causing the steam turbine generator condenser to underperform. The plant was losing 1.3 MW and 9 Btu/kWh per unit and, had the issue been left unaddressed, it could have led to a potential annual loss of more than $600,000.
Bringing forward a water wash
- Turbine performance was slowly degrading during the peak generating season, resulting in a loss of 2.0 MW and 200 Btu/kWh. By taking a short outage to perform the water wash, the plant avoided lost generation worth of over $300,000.
So, not only did we bring to light where the plant’s systems were underperforming, our comprehensive engineering analysis showed the way to significant cost savings.