Breaking New Ground at Guernsey Power Station
Expert Operations & Maintenance for New Caithness Energy Power Plant
- Goals
-
- Reduce Forced Outage Rate
- Increase reliability
- Reduce Maintenance Spend
- Reduce Downtime
- Sectors
-
- Power generation
- Asset
-
- Operations and Maintenance
- Location
- Byesville, Ohio, US
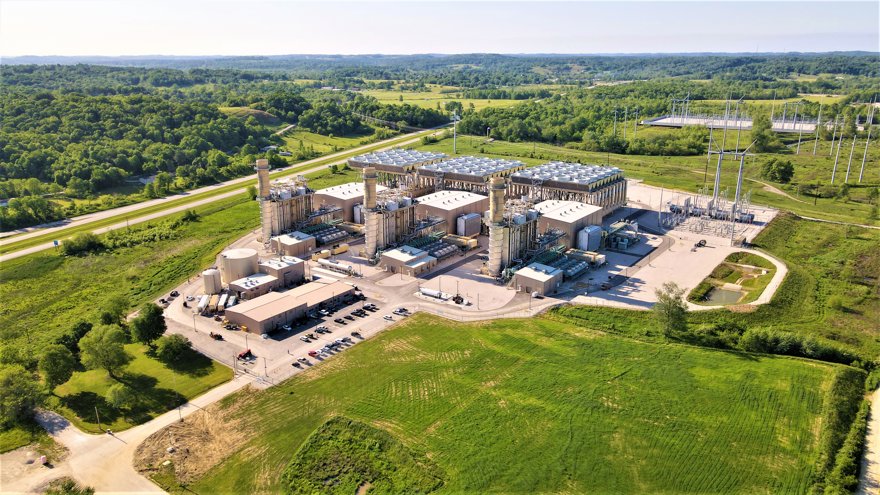
Building on Trust
Guernsey Power Station is no ordinary power generation facility.
A 1,875 MW combined-cycle power plant located in the heart of Ohio’s shale gas region, it generates enough electricity to supply an estimated 1.5 million homes in the US. With an efficiency rating of nearly 63%, it’s one of the most advanced and efficient power plants in the world. And thanks to its dry-cooling technology, it’s able to reduce water usage by as much as 95% compared with traditional power plants.
This impressive new-build facility is owned by Caithness Energy, L.L.C. – an independent power producer that specializes in the development, acquisition, operation, and management of renewable energy and natural gas power projects.
Caithness Energy performed all the construction and commissioning management services for the site. But when it came to operations and maintenance (O&M) of the facility, they turned to an independent service provider they knew they could rely on.
Back in 2018, when Caithness Energy was commissioning a 1,105 MW combined cycle power plant in Salem Township, Pennsylvania – Caithness Moxie Freedom Generating Station – they had contracted EthosEnergy to provide comprehensive third-party O&M care, custody, and control (CCC). That included commercial mobilization.
Building on that success, Caithness Energy placed their trust and confidence in our O&M services again.
Guernsey Power Station in a (111-acre) nutshell
The facility hosts three single-shaft power blocks, balance of plant (BOP) equipment, 230 and 765 kV switch yard, and a quarter of a mile of 765 kV transmission line.
Each power block is fueled by natural gas and a GE-supplied power train that consists of a 7HA.02 gas turbine, W84 generator, A650 steam turbine, and a heat recovery steam generator with supplemental duct firing. The single-shaft arrangement has a self-synchro-shifting (SSS) clutch to help increase flexibility. Almost unique for a power plant, the BOP equipment includes single-phase autotransformers stepping up power from 230 to 765kV.
Just under 4% of the nation’s gas passes through the property along a 1,200 mile 42-inch pipeline. Tapping directly onto this removes the need for costly gas pipelines. The plant also benefits from direct access to existing overhead transmission lines that traverse the property, a railroad spur, and two major interstates. These existing infrastructures made the site attractive to developers.
Not only has Guernsey Power Station been able to shrink its water usage, but 15 of its 111 acres are designated as protected wetlands.
Due to its enormous generating capacity, Guernsey Power Station is registered as a NERC Critical Infrastructure Protection (CIP) Medium Impact designated facility, making its presence on the grid even more important.
Full-time staffing and training in near record time
Construction began in September 2019. At its peak, over 1,000 employees, contractors, sub-contractors, and owner representatives were on site.
The first EthosEnergy employee on site was our Facility Manager, arriving in February 2021. Fast forward to April, we had hired most of the managers: the Maintenance Manager, Operations Manager, Plant Administrator, and HSE Manager, and drafted a comprehensive plan of actions and milestones.
We then completed the process of getting the hourly employees on board in near record time. From starting interviews, it took just over two and a half months for us to appoint all 24 operations and maintenance personnel. It helped that we had a strong pool of local candidates to choose from due to nearby coal and natural gas generating facilities, as well as oil and gas operations. In the end, the average power plant experience level hired was just over 17 years.
The employees were put through extensive training – both on and off site – in the classroom and in the field, from September 2021 through January 2022.
We then integrated approximately 60% of the operations team with the Engineering, Procurement and Construction (EPC) contractor’s commissioning team where they assisted with system punch list identification and mechanical completeness walkdowns. They also aligned systems up for the first time and participated in start-up and shutdowns of systems and equipment from the field and control room settings.
Dotting all the I’s and crossing all the T’s
We spent a considerable amount of time getting the facility ready by front-loading important tasks that was essential to successfully achieving commercial operation.
To do so, we generated over 240 site-specific procedures using OEM and industry guidelines, coupled with years of employee experience. Many of these procedures were written to govern administrative, maintenance, operations, safety, environmental and emergency response instructional and guidance directives. Others were tried and tested administrative and HSSE procedures developed by our central operations support team that have been proven across our generating fleet.
We also developed a comprehensive mobilization plan. This served as our strategic blueprint for making sure we were ready to take care, custody, and control of the facility. It consisted of 746 individual tasks and assignments. When the team arrived on site, we started working methodically through the plan to keep us centered and aligned. And once again, the team at site were supported by the central support team, including a team of experts regarding NERC, operations, maintenance, HSSE, information technology, and human resources which continues through the duration of the CCC contract.
By April 2023, when we officially assumed commercial care, custody, and control of the facility, we had completed 99.8% of the plan tasks, as well as numerous tasks that aren’t typically completed until well into commercial operation.
Safety first
Construction and commissioning can be one of the most dangerous periods on a power plant project. A lot goes on that you would not typically see when a plant is up and running. Objects fly overhead. Heavy machinery runs around on the ground. Systems and equipment pressured up and energized for the first time. Everybody must maintain constant safety vigilance.
But if there’s one value we prize above all others – the one that puts the ethos in EthosEnergy – it’s safety.
Our record at Guernsey Power Station bears this out.
Before taking care, custody, and control of the facility, we went through a rigorous and comprehensive HSE assessment. And to date, we have performed nearly 165,000 safe work hours with zero recordable injuries or lost time incidents.
A remarkable achievement. And one we’re immensely proud of.
Key Results
- A highly skilled and talent staff was hired.
- Operations and maintenance team mobilized in record time.
- Over 240 procedures developed and implemented.
- 746 individual mobilization tasks generated leading to a 99.8% completion rate by the time we achieved commercial operation.
- 165,000 safe hours worked with no recordable injuries or lost time incidents.
Sales
Looking for more?
We have a wide portfolio of case studies with proven results in the power generation industry. View our hand picked examples to read how our maintenance services can help reduce forced outage rate.